说明:
“双碳”目标下,政策对于汽车百公里油耗提出要求。2020 年 10 月,中国 汽车工程学会牵头组织编制的《节能与新能源汽车技术路线》发布,对各种 类型的汽车每百公里油耗提出了要求,预计在 2030 年,我国新能源汽车占到总销 量 40%,乘用车百公里油耗达 3.2L,响应“双碳”目标。从燃油车角度来看,汽 车的平均油耗与整车质量呈正相关,汽车轻量化对于降低传统车油耗具有积极促 进作用。据研究数据,汽车重量每减轻 10%,最多可实现节油 5-10%;汽车整备 质量每减少 100 千克,百公里油耗可降低 0.3-0.6 升。 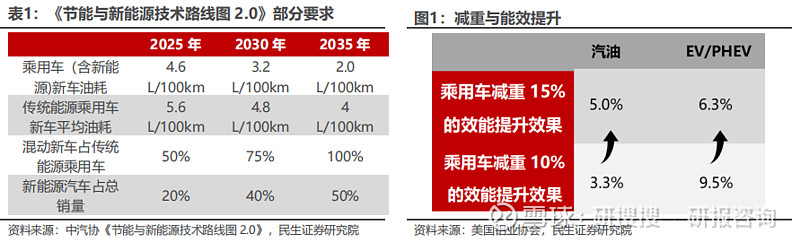
国内汽车新能源化进程提速,据乘联会数据, 2017-2021 年,中国新能源汽车的市场渗透率从 2.7%大幅增长至 13.4%,渗透 率于 2022 年达到历史新高 27.6%。新能源渗透率持续走高,但“里程焦虑”仍限 制消费者购买新能源汽车。一般来说,传统内燃机车加满油可以行驶 500 公里以 上,而大部分电动车的续航里程在 300-500 公里左右,仍然存在差距。解决里程 焦虑包括: 1)提升电池能力密度。《我国制造 2025》明确了动力锂电池的展开 规划:2020 年,电池能量密度抵达 300Wh/kg;2025 年,电池能量密度抵达 400Wh/kg;2030 年,电池能量密度抵达 500Wh/kg。电池能量密度短期内较难 提升 2)增加电池组数量并减重。与传统能源汽车相比,新能源汽车由于搭载三 电系统,往往比燃油车重 10%,增加电池组数量可提升续航里程,但是电池组总 重达 900Kg,已占总车质量的 42.7%。综上,提升续航里程应最大化进行新能源汽车减重。 新能源汽车新增三电系统(电池、电机与电控),整车整备质量普遍高于传统 燃油车。据 DuckerFrontier 研究,由于减少了燃油车用发动机、传动系统以及其 他零部件,新能源车用铝量分别减少了 49/39/5kg;由于新增电池包、电驱动系 统等,新能源车在动力传动系统、电池包与车身结构件及其他零部件分别使单车用 铝量提高了 30/142/7kg,轻量化势在必行。 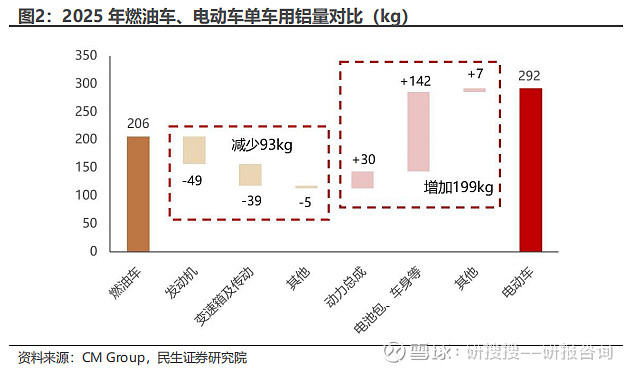
轻量化大势所趋,轻量化路径主要包括材料、工艺、结构三个方面,可从动力、 车身、底盘、内外饰等多个部位减重。材料方面选用铝合金、碳纤维等质地较轻的 材料进行制造可以实现降重,轻量化材料零部件除减重外还可以提升汽车性能,如 铝合金制造的各种零部件壳体的散热性能更好,镁合金制造汽车方向盘骨架柔韧 性更好,使用碳纤维材料制造刹车片可承受更高的热冲击,耐磨性好等。 另外,轻 量化材料相对钢铁而言,整体而言更加美观。为此,整车厂商有动力开发包括轻量 化材料在内的新材料,提升汽车性能、美观度等,实现品牌升级,提高议价能力。 在制造工艺上,使用激光焊接或液压成形技术,可以在工艺上减少零件的使用数量, 在不同部位连接处减少材料使用,从而减轻质量,结构优化则在保证强度的情况下 进行结构设计,从而减少质量。 三电系 2)结 构优化:电驱系统集成化(减速器、电机和电控从各自独立的壳体设计,到电机、 减速器壳体一体化和三大件壳体一体化)。随着更多功能集成到电驱动中,壳体也 将叠加更多的功能设计,例如,电机、电控及减速器均需冷却系统,因此,壳体的 设计需要考虑冷却管路的设计和布局,对壳体供应商的产品提出了较高的要求。 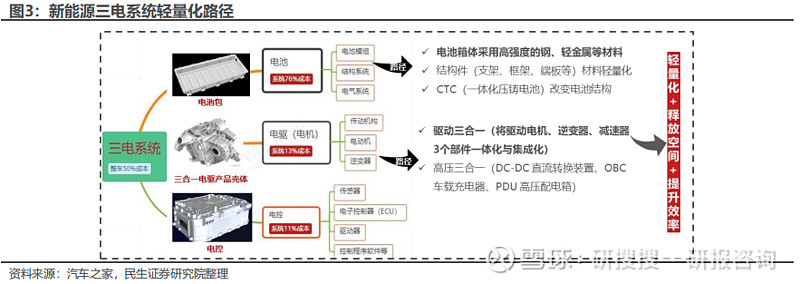
国内外企业致力于轻量化制造。结合汽车轻量化节能、减重、降本的优势,在 中国新能源汽车快速渗透的背景下,轻量化是汽车行业的大势所趋。车企轻量化方 向包括: 3)使用一体化压铸工艺。汽车零部件每个环节都能实现轻 量化制造,国内外主流零部件公司均在致力于轻量化制造。 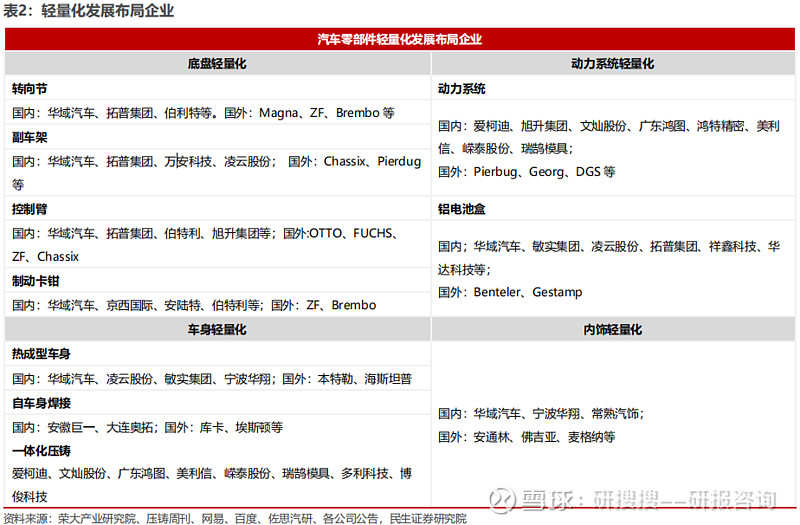
据星源卓镁招股说明书,从应用上来看,钢铁、铝合金和塑料是汽车上使用最 多的三大类材料,按重量计算,2022 年三类材料占整车的比例合计约为 80%, 其中钢铁占 62%,铝合金和塑料占比均为 8%至 10%,镁合金在汽车上的应用比 例仅约为 0.3%。 轻量化材料势在必行,轻金属用量持续提升,均衡成本与收益是关键。轻金属 及复合材料价格相对钢铁更加昂贵,大量使用会带来成本的上升,以白车身为例, 钢车身重量在 375kg 左右,假设钢价为 5 元/kg(参考爱采购钢价),白车身材 料价格约为 1875 元;如果使用铝合金代替钢,其重量为 230kg,减重比例接近 40%,以 20 元/kg(参考爱采购铝合金价)的价格计算,白车身材料价格约为 4600 元。因此,厂商需综合考虑使用轻量化材料带来的成本上升,以及由于重量下降带 来的收益。 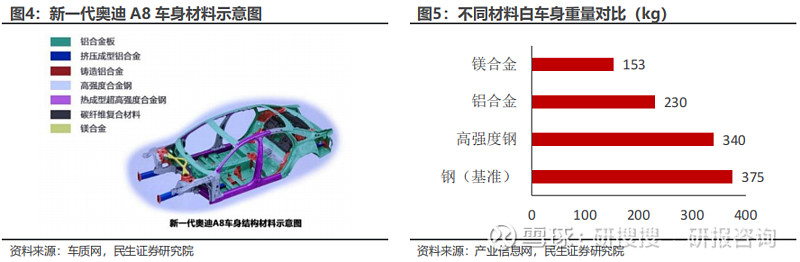
2.1 铝合金材料性能优良,单车用铝量持续提升 铝合金是现阶段较好的轻量化材料之一。铝合金的性能、密度、成本和可加工 性等综合优势突出: 1)密度上,高强度钢的密度是 7.87g/cm³,而铝合金的密度 是 2.7g/cm³,传统汽车中车身约占整车重量的 30%-40%,用高强度钢替代普通 钢材能减重约 11%,而如果采用铝合金,减重效果约为高强度钢的 2.25 倍,镁合 金减重效果优于铝,但受限于镁自身化学性质活跃、不如铝合金耐腐蚀,加工生产 成本高昂,目前在汽车行业应用较少 2)性能上,铝合金塑性优良,工业生产中 的铸、锻、冲工艺均能适用,适于广泛应用于压力铸造工艺,其余材料如镁合金面 临价格较高及高温抗蠕变问题,碳纤维是脆性材料,具备高昂成本,难以普及,高 强钢凭借其高强度应用于车身关键部位,但减重效果有限 3)性价比方面,铝合 金的价格约为高强度钢的 6.7 倍,镁的价格约为高强度钢的 16.7 倍。因此在综合 性能、成本、制造技术和机械性能等方面都表现出色。铝合金加速代替汽车钢材零 部件,例如气缸体、变速器壳、转向机壳、发动机罩等等,绝对减重均可达 70kg。 当前众多主流车型均采用全铝车身,前后悬架大部分材料也采用铝合金,用铝化程 度越来越高,最大程度实现轻量化制造。 im电竞
|